Efektywne zarządzanie wilgocią w systemach sprężonego powietrza: wybór odwadniaczy, filtrów i osuszaczy
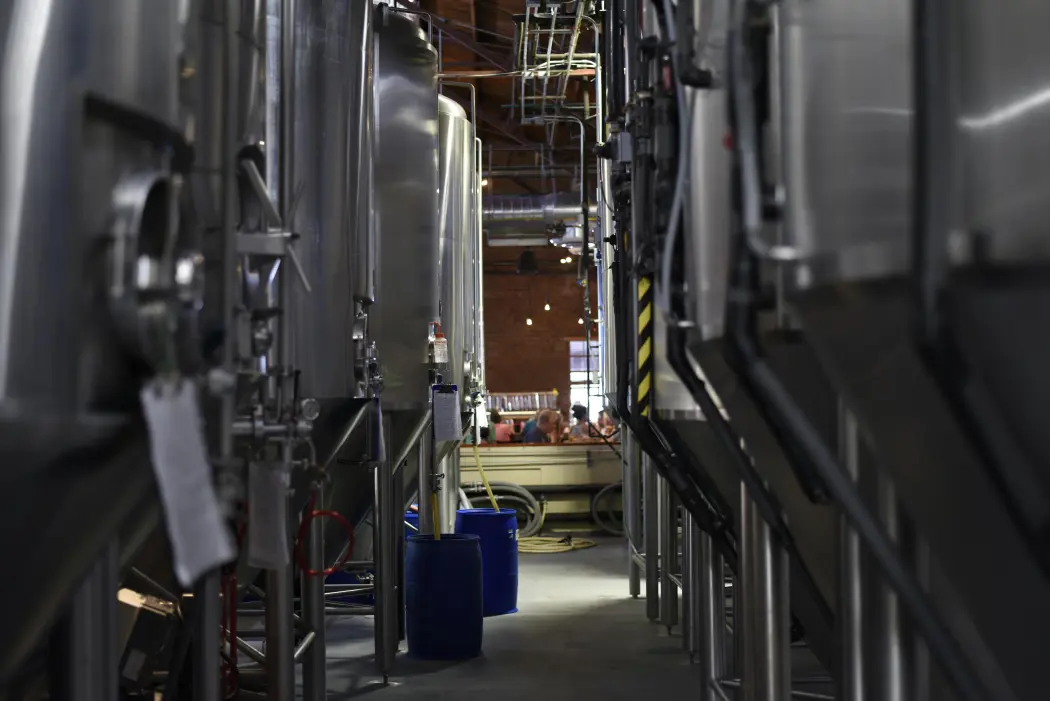
Nowoczesne systemy pneumatyczne, niezależnie od skali zastosowania, wymagają precyzyjnie dobranego osprzętu oczyszczającego sprężone powietrze. Trzy kluczowe elementy odwadniacze, filtry powietrza oraz osuszacze stanowią fundament efektywnej kontroli wilgoci i zanieczyszczeń, warunkując tym samym niezawodność, wydajność oraz długowieczność całej instalacji. Artykuł przedstawia zaawansowaną analizę tych komponentów, oferując specjalistyczną wiedzę niezbędną przy ich właściwym doborze i konserwacji.
Znaczenie kontroli wilgoci w instalacjach pneumatycznych
Geneza problemu kondensatu
Podczas procesu sprężania powietrza następuje znaczący wzrost jego temperatury. W fazie ochładzania, nieunikniony staje się proces kondensacji pary wodnej zawartej w powietrzu atmosferycznym. Powstający kondensat mieszanina wody i mikroskopijnych cząstek oleju stanowi poważne zagrożenie dla integralności całego systemu pneumatycznego, szczególnie gdy jego ilość przekracza dopuszczalne normy dla danego zastosowania.
Potencjalne konsekwencje niekontrolowanej wilgoci
Obecność nadmiernej ilości kondensatu w systemie sprężonego powietrza inicjuje szereg niekorzystnych procesów:
- Korozja elektrochemiczna elementów metalowych, prowadząca do postępującej degradacji rurociągów, zbiorników i urządzeń wykonawczych
- Nieprawidłowości w funkcjonowaniu zaworów, siłowników i innych komponentów pneumatycznych
- Przyspieszone zużycie elementów ruchomych w narzędziach pneumatycznych
- Kontaminacja produktów końcowych szczególnie krytyczna w przemyśle spożywczym, farmaceutycznym i elektronicznym
- Zwiększenie oporów przepływu w rurociągach, skutkujące spadkiem efektywności energetycznej całego systemu
Odwadniacze: zasada działania i kryteria wyboru
Techniczna charakterystyka odwadniaczy
Odwadniacz to wyspecjalizowane urządzenie separujące i odprowadzające kondensat ze strumienia sprężonego powietrza. Ich działanie opiera się na wykorzystaniu różnic fizykochemicznych między fazą gazową (sprężone powietrze) a fazą ciekłą (kondensat). Proces separacji musi przebiegać bez istotnych strat ciśnienia w systemie, co wymaga precyzyjnie zaprojektowanej konstrukcji hydrodynamicznej urządzenia.
Klasyfikacja odwadniaczy według mechanizmu działania
Konstrukcja odwadniacza dzwonowego wykorzystuje zasadę hydrostatyczną. Kluczowym elementem jest pływający dzwon, reagujący na zmiany poziomu zgromadzonego kondensatu:
- Przy niskim poziomie kondensatu dzwon opada, zamykając zawór odprowadzający
- Gdy poziom kondensatu wzrasta, siła wyporu powoduje podniesienie dzwonu, otwierając drogę odpływu
- Ciśnienie systemowe wypycha kondensat przez otwarty zawór
- Po odprowadzeniu kondensatu dzwon ponownie opada, zamykając zawór
Odwadniacze dzwonowe wykazują wysoką odporność na uderzenia hydrauliczne oraz zanieczyszczenia mechaniczne, co czyni je optymalnym rozwiązaniem dla systemów przemysłowych pracujących w trudnych warunkach. Ich wydajność jest proporcjonalna do objętości dzwonu, co należy uwzględnić przy doborze do konkretnej instalacji.
Odwadniacze termodynamiczne
Te zaawansowane technicznie urządzenia wykorzystują zjawiska termodynamiczne zachodzące przy przepływie sprężonego powietrza:
- W fazie początkowej zimny kondensat przepływa pod tarczą odwadniacza
- Przepływ gorącego sprężonego powietrza powoduje wzrost temperatury i ciśnienia pod tarczą
- Różnica ciśnień dociska tarczę do gniazda, zamykając przepływ
- Przy ochłodzeniu tarczy ciśnienie spada, umożliwiając ponowne otwarcie
Kompaktowa konstrukcja bez elementów ruchomych zapewnia wyjątkową niezawodność w systemach wysokociśnieniowych. Odwadniacze termodynamiczne charakteryzują się szybką reakcją i mogą być montowane w dowolnej pozycji, co stanowi istotną zaletę w ograniczonych przestrzeniach.
Strategiczne kryteria doboru odwadniacza
Optymalny wybór typu odwadniacza powinien uwzględniać następujące parametry techniczne:
- Przepustowość wyrażona jako maksymalna ilość kondensatu możliwa do odprowadzenia w jednostce czasu
- Zakres ciśnień roboczych zgodny z parametrami pracy kompresora
- Odporność na zanieczyszczenia szczególnie istotna w środowiskach przemysłowych
- Efektywność energetyczna minimalizacja strat ciśnienia i sprężonego powietrza
- Niezawodność w danych warunkach eksploatacyjnych temperatura otoczenia, wilgotność, wibracje
Filtry powietrza: kompleksowa ochrona systemu pneumatycznego
Wielostopniowa filtracja powietrza
Skuteczny system filtracji sprężonego powietrza wymaga implementacji rozwiązań wielostopniowych, gdzie każdy element realizuje określone zadanie w procesie oczyszczania:
- Filtry wstępne (5-40 μm) eliminacja większych cząstek stałych i wstępna separacja kondensatu
- Filtry dokładne (1-5 μm) zatrzymywanie mikrocząstek i dalsze usuwanie wilgoci
- Filtry submikronowe (0,01-1 μm) zatrzymywanie najdrobniejszych zanieczyszczeń, w tym bakterii i aerozoli olejowych
- Filtry z węglem aktywnym absorpcja zapachów i szkodliwych oparów
Zaawansowane technologie filtracyjne
Współczesne filtry wykorzystują różnorodne mechanizmy separacji zanieczyszczeń:
- Filtracja mechaniczna fizyczne zatrzymywanie cząstek większych niż średnica porów materiału filtracyjnego
- Filtracja inercyjna wykorzystanie bezwładności cząstek, które nie są w stanie podążać za zmianami kierunku przepływu powietrza
- Filtracja dyfuzyjna zatrzymywanie najmniejszych cząstek wskutek ich chaotycznego ruchu i przyciągania elektrostatycznego
- Koalescencja łączenie mikroskopijnych kropel cieczy w większe krople, które łatwiej podlegają separacji grawitacyjnej
Parametry techniczne determinujące wybór filtra
Przy doborze systemu filtracji należy uwzględnić:
- Klasę czystości powietrza wymaganą dla danej aplikacji (zgodnie z normą ISO 8573-1)
- Wydajność przepływową dopasowaną do maksymalnego przepływu w systemie
- Spadek ciśnienia nie przekraczający wartości krytycznych dla wydajności systemu
- Pojemność zatrzymywania zanieczyszczeń wpływającą na częstotliwość wymiany wkładów
- Efektywność separacji kondensatu szczególnie istotną przy wysokiej wilgotności powietrza wlotowego
Osuszacze: technologie eliminacji wilgoci resztkowej
Osuszacze chłodnicze
Działanie osuszaczy chłodniczych opiera się na obniżeniu temperatury sprężonego powietrza poniżej punktu rosy, co powoduje kondensację zawartej w nim pary wodnej:
- Sprężone powietrze jest schładzane w wymienniku ciepła do temperatury około 3-5°C
- Skroplona wilgoć jest odprowadzana przez automatyczny system drenażu
- Osuszone powietrze jest podgrzewane w wymienniku ciepła przez ciepłe powietrze wlotowe
Osuszacze chłodnicze są ekonomicznym rozwiązaniem dla standardowych zastosowań przemysłowych, osiągając punkt rosy na poziomie +3°C.
Osuszacze adsorpcyjne
Te zaawansowane urządzenia wykorzystują właściwości higroskopijne materiałów, takich jak żel krzemionkowy czy tlenek aluminium, do głębokiego osuszania powietrza:
- Sprężone powietrze przepływa przez złoże adsorpcyjne, które wiąże cząsteczki wody
- Regeneracja złoża następuje poprzez obniżenie ciśnienia i przedmuch suchym powietrzem
- System dwuwieżowy zapewnia ciągłość pracy podczas gdy jedno złoże pracuje, drugie jest regenerowane
Osuszacze adsorpcyjne mogą osiągać punkt rosy nawet -70°C, co czyni je niezbędnymi w aplikacjach wymagających ekstremalnie suchego powietrza, jak produkcja elektroniki czy procesy farmaceutyczne.
Optymalna konfiguracja i konserwacja systemu uzdatniania powietrza
Strategiczne rozmieszczenie komponentów
Efektywność systemu uzdatniania sprężonego powietrza zależy od właściwej sekwencji montażu poszczególnych elementów:
- Wstępny separator kondensatu bezpośrednio za chłodnicą końcową kompresora
- Zbiornik powietrza wyposażony w odwadniacz automatyczny
- Filtr wstępny przed osuszaczem
- Osuszacz centralna jednostka usuwająca wilgoć resztkową
- Filtr dokładny za osuszaczem
- Filtr submikronowy/z węglem aktywnym bezpośrednio przed punktami poboru wymagającymi najwyższej czystości powietrza
Zaawansowany program konserwacji prewencyjnej
Utrzymanie optymalnych parametrów pracy wymaga systematycznych działań konserwacyjnych:
- Kontrola odwadniaczy weryfikacja poprawności odprowadzania kondensatu (codziennie)
- Sprawdzanie wskaźników różnicy ciśnień na filtrach identyfikacja stopnia zanieczyszczenia wkładów (tygodniowo)
- Czyszczenie wymienników ciepła osuszaczy chłodniczych zapewnienie efektywnej wymiany ciepła (kwartalnie)
- Analiza jakości sprężonego powietrza weryfikacja zgodności z wymaganą klasą czystości (półrocznie)
- Kompleksowy przegląd techniczny ocena stanu wszystkich komponentów systemu (rocznie)
Profesjonalnie zaprojektowany system uzdatniania sprężonego powietrza, obejmujący właściwie dobrane odwadniacze, filtry i osuszacze, stanowi fundament efektywności operacyjnej instalacji pneumatycznej. Inwestycja w wysokiej jakości komponenty oraz ich systematyczna konserwacja przekłada się bezpośrednio na minimalizację kosztów eksploatacyjnych, wydłużenie żywotności narzędzi pneumatycznych oraz zapewnienie wymaganej jakości sprężonego powietrza dla procesów produkcyjnych.
Autor: Artykuł partnera